Das Wichtigste in Kürze
- Laserschneiden von Rohren ist ein hochpräzises, kontaktloses Verfahren, das sich für viele Materialien und Rohrformen eignet.
- Es ersetzt klassische Methoden wie Sägen und Fräsen und bietet zahlreiche Vorteile: höhere Präzision, schnellere Bearbeitung, weniger Nacharbeit, geringere Kosten und bessere Automatisierung.
- Besonders bei komplexen Formen und hohen Stückzahlen ist das Laserschneiden wirtschaftlich und effizient.
- Durch die Integration in digitale Prozesse und Automatisierung wird die Fertigung moderner, flexibler und leistungsfähiger.
Inhaltsverzeichnis
Anzeige – Dieser Beitrag wurde im Rahmen einer bezahlten Kooperation veröffentlicht.
Einleitung
Die Fertigungsbranche entwickelt sich stetig weiter, immer auf der Suche nach mehr Genauigkeit, Wirtschaftlichkeit und effizienten Abläufen. Viele Betriebe schneiden ihre Rohre noch per Hand mit klassischen Methoden wie Sägen und Fräsen oder geben diese Aufgaben nach außen ab.
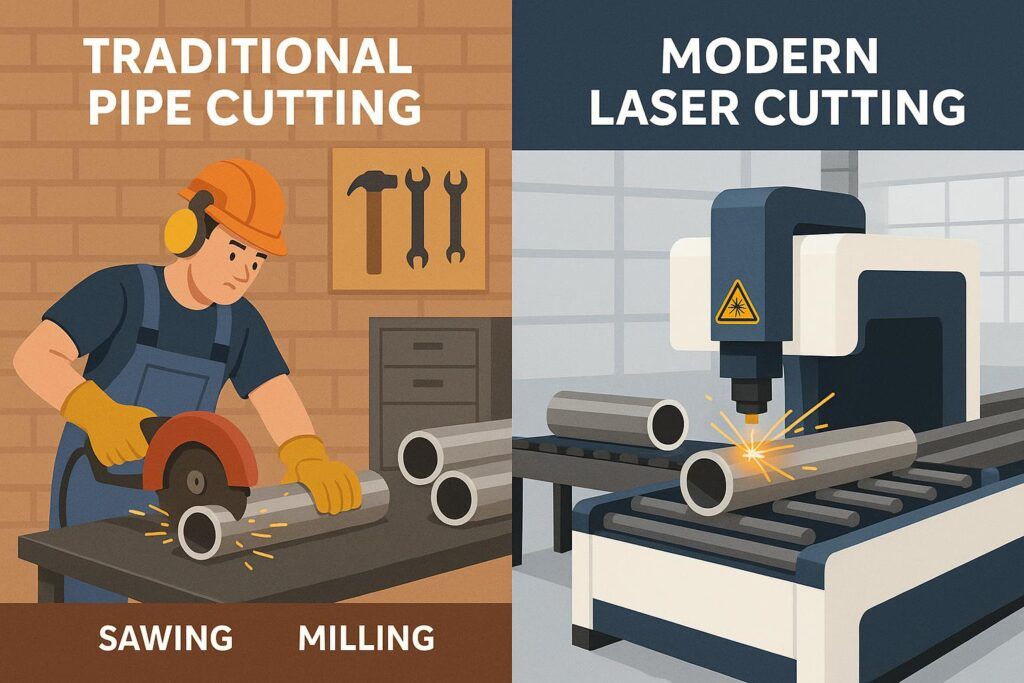
Doch in den letzten Jahren hat das Laserschneiden von Rohren einen echten Durchbruch in der Produktion geschafft. Dieses moderne Verfahren bietet eine Vielzahl an Vorteilen, die mit herkömmlichen Techniken kaum erreichbar sind.
Dank digitaler Prozesse und neuer Maschinen ist das manuelle Schneiden oder die Vergabe an andere Firmen oft nicht mehr zeitgemäß.
Was ist das Laserschneiden von Rohren?
Beim Laserschneiden wird ein Rohr oder Profil mit einem konzentrierten Laserstrahl bearbeitet. Der Laser schneidet das Material entlang einer festgelegten Linie, indem es lokal schmilzt, verdampft oder verbrennt.
Diese Technik funktioniert nicht nur bei flachen Blechen, sondern auch bei dreidimensionalen Körpern wie Rohren komplett kontaktlos und äußerst präzise.
Grundlagen und Ablauf
Die Technik wandelt elektrische Energie in einen starken Lichtstrahl um. Über Spiegel oder Glasfasern gelangt dieser Strahl zum Schneidkopf und wird dort auf einen winzigen Punkt gebündelt. An dieser Stelle schmilzt das Material durch die große Energie. Gleichzeitig wird meist Stickstoff oder Sauerstoff zugeführt, der die flüssigen Reste aus der Schnittfuge bläst und so eine saubere Kante hinterlässt.
Da das Verfahren ohne Berührung abläuft, entstehen keine Druckstellen oder Verformungen am Material – ein großer Unterschied zu mechanischen Methoden, bei denen das Werkzeug direkt arbeitet.
Welche Rohre und Materialien sind geeignet?
Das Laserschneiden ist sehr vielseitig. Man kann Metalle wie Stahl, Edelstahl, Aluminium und Kupfer sowie auch einige Kunststoffe, Glas oder Keramik schneiden – je nach Material sind die Anforderungen verschieden.
Nicht nur runde Rohre sind möglich: Auch eckige, rechteckige, ovale und ausgefallen geformte Profile können bearbeitet werden. Moderne Maschinen bewältigen viele Rohrgrößen und verschiedene Wandstärken. So ist das Verfahren in vielen Industriebereichen nutzbar.
Wie unterscheidet sich das Laserschneiden von anderen Methoden?
Der echte Unterschied zeigt sich im Vergleich zu klassischen Arbeitsweisen wie Sägen, Fräsen oder Stanzen.
Sägen, Fräsen, Stanzen: Die Unterschiede
Mechanische Methoden arbeiten immer mit direktem Kontakt. Zum Beispiel schlägt beim Sägen das Sägeblatt auf das Material. Speziell bei dickeren Werkstoffen entstehen dann oft Grate, Verformungen oder raue Schnittkanten, sodass nachgearbeitet werden muss.
Auch Fräsen oder Stanzen hinterlassen Spuren und sind bei komplizierten Aufgaben meist auf mehrere Durchgänge angewiesen. Der Laser hingegen schneidet das Material punktgenau und ohne jede Kraftaufnahme. Schnittkanten werden glatt und sauber, meistens ohne Nacharbeit.
Selbst aufwendige Formen, Bohrungen oder Schlitze erledigt der Laser in einem einzigen Arbeitsschritt – was mit handbetriebenen Maschinen viel länger und umständlicher dauern würde.
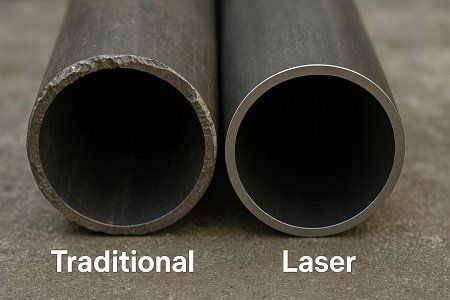
Effizienz und Kosten
Eine Laseranlage kostet am Anfang mehr als eine einfache Säge oder Fräse. Doch aufs Ganze gesehen rechnet sich das Lasern schnell, besonders wenn viele Teile oder spezielle Formen gebraucht werden. Werkzeuge nutzen sich nicht ab, was gerade bei härteren Materialien wie Edelstahl Kosten spart.
Der Laser arbeitet sehr schnell, und weil Schneiden, Bohren und Markieren oft in einem Durchgang erledigt werden, schrumpft die Zeit je Teil deutlich. Dank der dünnen Schnittfuge bleibt mehr Material übrig, was vor allem bei teuren Rohren wichtig ist. Bei überraschend kleinen Mengen – zum Beispiel bei großen oder dicken Rohren – kann das Lasern günstiger sein als das Sägen.
Laserschneiden und bessere Abläufe in der Fertigung
Das Laserschneiden ist mehr als nur ein schneller oder genauer Schnitt: Es macht Abläufe in der Fertigung viel effizienter.
Schnellere Arbeitsabläufe
Früher mussten Rohre oft an mehreren Stationen gesägt, gebohrt, gefräst und entgratet werden. Heute kann ein Rohrlaserzentrum all diese Bearbeitungsschritte hintereinander in einer Maschine machen.
Dadurch fällt nicht nur viel Arbeitszeit weg (Einsparungen von bis zu 49% möglich), auch das Hin- und Hertragen sowie Zwischenlagerung entfallen. Automatische Zuführung und programmierte Abläufe sorgen dafür, dass weniger Personen und weniger Bereiche beteiligt sind, die Fertigung wird flüssiger und übersichtlicher.
Weniger Fehler und Ausschuss
Weil der Laser äußerst genau arbeitet, gibt es weniger Fehler und falsch geschnittene Stücke. Die Schnittflächen sind glatt und frei von Graten, Nacharbeiten sind selten nötig. Weitere Extras wie exakt gesetzte Hilfslinien, Zapfen oder Stege helfen beim späteren Zusammenbauen und vermeiden Einbaufehler.
Auch Gravuren und Markierungen lassen sich direkt beim Schneiden aufbringen – das macht das Sortieren, Montieren und Zuordnen auf der Baustelle viel leichter und senkt das Risiko von Verwechslungen.
Die 7 wichtigsten Vorteile des Laserschneidens von Rohren
Die wichtigsten Pluspunkte beim Laserschneiden von Rohren sind:
1. Sehr hohe Genauigkeit und gleichbleibende Qualität
Der Laser ermöglicht Schnitte mit Toleranzen im Bereich von tausendstel Millimetern. Die Kanten werden sauber, glatt und ohne Grate. Diese Qualität kann immer wieder zuverlässig erreicht werden.
2. Schnelle Bearbeitung
Laserschneiden geht sehr schnell, da viele Bearbeitungsschritte kombiniert werden können. Die Zeit vom Rohmaterial zum fertigen Teil verringert sich stark.
3. Hohe Flexibilität bei komplizierten Formen
Mit dem Laser sind fast alle gewünschten Konturen, Bohrungen, Schlitze und sogar dreidimensionale Ausschnitte möglich – auch schräge oder gebogene Schnitte dank spezieller 5-Achs-Köpfe.
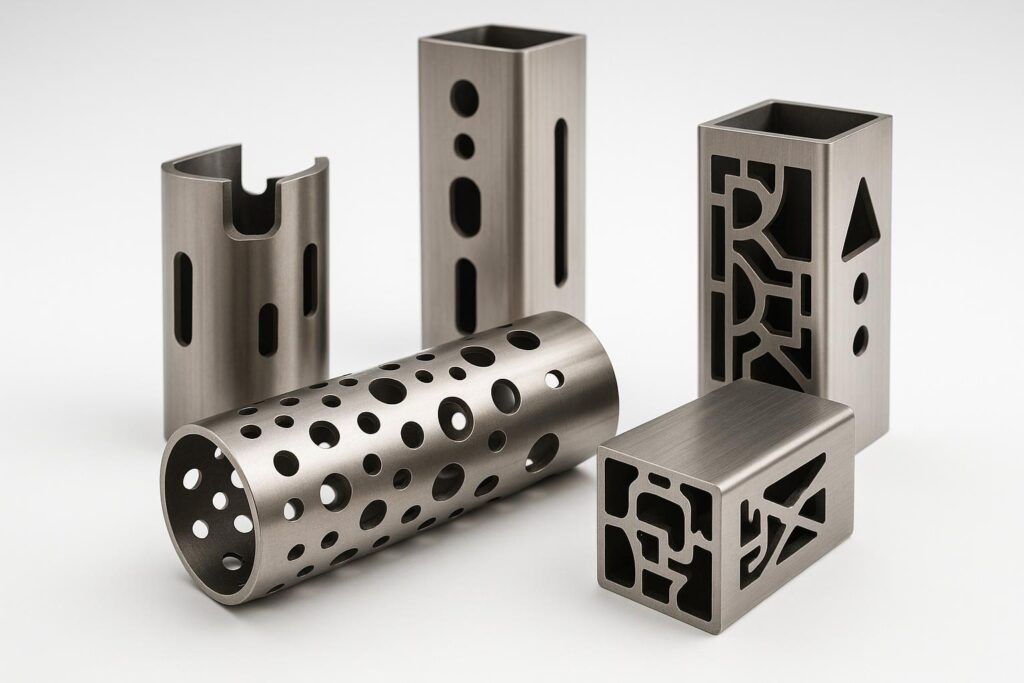
4. Weniger Nacharbeit, weniger Materialverlust
Weil die Schnittkanten glatt und sauber sind, entfällt meist das Entgraten oder Schleifen. Außerdem ist der Schnitt sehr schmal, wodurch kaum Material verloren geht. Durch geschickte Platzierung im Rohr wird auch der Verschnitt reduziert.
5. Gute Einbindung in automatisierte Prozesse
Rohrlaserzentren sind automatisiert und programmierbar. Material wird automatisch zugeführt, verschiedene Bearbeitungen direkt integriert – das kann alte Fertigungsstraßen überflüssig machen.
6. Geringere Produktionskosten
Durch weniger Material- und Werkzeugverbrauch, gesparte Bearbeitungszeit und geringeren Aufwand beim Transport und in der Montage sinken die Herstellungskosten – Einsparungen von bis zu 10% sind möglich.
7. Bessere Nutzung von Lager und Personal
Da weniger Zwischenlagerung und Bearbeitung nötig sind, braucht man weniger Platz im Lager und weniger Mitarbeitende in der Fertigung. Abteilungen arbeiten enger zusammen. So werden Kapazitäten frei.
Das Laserschneiden von Rohren hat die Metallbearbeitung grundlegend verändert. Es ist heute sowohl für die schnelle Herstellung von Standardteilen als auch für ausgefallene Rohrformen, die früher nicht möglich waren, die beste Wahl.
Zwar sind die Anschaffungskosten für eine Laseranlage hoch und auch der Energie- sowie Gasverbrauch sollte bedacht werden. Dennoch: Für viele Anwendungen überwiegen die Vorteile klar. Die Möglichkeit, Bauteile direkt mit Einbauhilfen oder Markierungen zu versehen, spart Zeit und Kosten bei der Montage und kann sogar das Schweißen ersetzen.
Durch moderne Online-Plattformen ist es inzwischen einfach möglich, Konstruktionsdaten hochzuladen und schnell ein Angebot für präzise gelaserte Rohrteile zu bekommen – das beschleunigt die Produktion vom ersten Entwurf bis zum fertigen Bauteil deutlich.
Übersichtstabelle: 7 Vorteile des Laserschneidens von Rohren
Vorteil | Beschreibung | Nutzen für die Fertigung |
---|---|---|
1. Sehr hohe Genauigkeit | Schnitte mit Toleranzen im Tausendstel-Millimeter-Bereich, saubere Kanten | Gleichbleibende, hohe Qualität |
2. Schnelle Bearbeitung | Mehrere Bearbeitungsschritte in einem Durchgang möglich | Deutlich kürzere Produktionszeiten |
3. Hohe Flexibilität bei Formen | Komplizierte Konturen, Bohrungen und 3D-Ausschnitte, auch schräge Schnitte | Vielseitig einsetzbar, neue Designmöglichkeiten |
4. Weniger Nacharbeit & Materialverlust | Glatte Schnittkanten, schmaler Schnitt, weniger Verschnitt | Geringere Kosten und weniger Materialbedarf |
5. Automatisierung & Integration | Automatische Zuführung, programmierbare Abläufe | Effizientere Fertigungsprozesse |
6. Geringere Produktionskosten | Weniger Werkzeugverschleiß, weniger Personal und Lagerbedarf, geringerer Zeitaufwand | Bis zu 10% Kosteneinsparung |
7. Optimale Nutzung von Lager & Personal | Weniger Zwischenlagerung, weniger Personal, bessere Zusammenarbeit der Abteilungen | Kapazitäten werden frei, effizientere Abläufe |
Fazit über Laserschneiden von Rohren
Das Laserschneiden von Rohren revolutioniert die moderne Fertigung: Es bietet eine bislang unerreichte Präzision, Flexibilität und Effizienz. Trotz höherer Anfangsinvestitionen rechnet sich das Verfahren schnell durch geringere Produktionskosten, weniger Materialverlust und optimierte Abläufe. Für alle, die Wert auf Qualität, Wirtschaftlichkeit und moderne Fertigung legen, ist das Laserschneiden von Rohren heute die erste Wahl – egal ob für Standardteile oder individuelle Sonderlösungen.
https://bayreuth-region.de/industrie-und-produktion-in-bayreuth/